Dew point monitoring in plastic granulate dryers
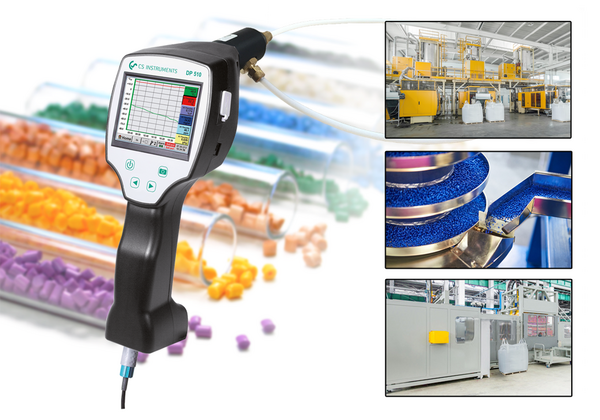
If plastic granules are not optimally dried before injection molding, this can have a variety of negative effects on the product. For example, processing plastic granules that are too moist can lead to quality problems in the product on the one hand, but also to problems in the injection molding process itself on the other.
During transport and storage, the plastic granules can absorb moisture, depending on the plastic. Many plastics themselves are hygroscopic and really attract moisture. The water vapor can even penetrate deep into the molecular structure, which is then referred to as core moisture. Environmental influences have the greatest influence here, and so the moisture content in the plastic granules also fluctuates depending on the season.
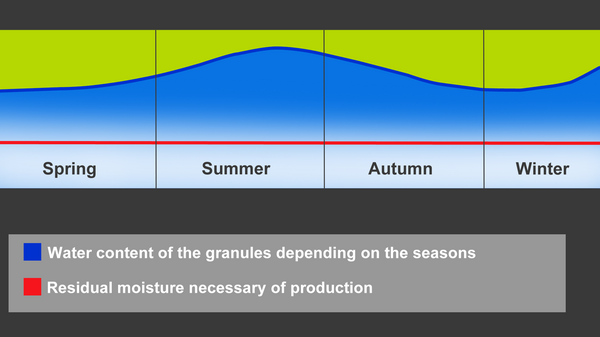
Moisture is deposited in the pores and on the surface of the granules, which can lead to quality problems during further processing in the injection molding process. Unwanted patterns, bubbles or cavities on the surface are the result. Quality losses such as blowholes can also occur inside the workpiece. Quality inspections are usually very time-consuming and destructive since it is not possible to simply look inside the molded part.
Process problems can also occur during injection molding. Problems such as vapor formation, foam formation, mold filling problems, or viscosity problems are not uncommon with improperly dried granules. The machine or mold can also be damaged, leading to downtime in the worst case.
Increasing quality requirements for plastic products make economical drying of the plastic granulate to be processed necessary and profitable. During drying, the dew point should ideally be in the range between -30…-60°Ctd, lower dew points are not necessary, and the drying process would then also become less economical. However, dew points that are too high are also undesirable, because above a dew point of -15°Ctd, a sufficient drying effect is no longer achieved.
Where previously a sample had to be analyzed in the laboratory, i.e. there was only a snapshot of the system, CS Instruments GmbH & Co. KG today comes up trumps with much more advanced solutions. Today, plastic granulate dryers can be monitored in real time by means of a permanently installed dew point meter, alarms can be switched, or other measures can be taken in the event of problems with the dryer. CS Instruments also boasts a mobile dew point meter specially developed for this application, which can be used easily and portably at various measuring points.