Measuring compressed air quality according to ISO 8573
In summary, a bulk material is a powdery, granular, or lumpy material that is present in a form in which it can be poured. Bulk solids can consist of many materials and are defined by particle size, bulk density, roughness, and temperature. For example, building materials such as gravel, cement and sand are bulk materials, but foodstuffs such as sugar, salt, coffee, and flour are also considered bulk materials.
The transport of these bulk materials requires special measures. A distinction is made between continuous and discontinuous transport. Continuous transport is ensured, for example, by means of hoses or pipes with compressed air as the conveying medium – so-called pneumatic conveying.
The optimization of pneumatic conveying systems is very popular today because a lot of energy can be saved. For conveying through pipes and hoses, either treated or untreated compressed air is used, depending on the bulk material. The amount of compressed air required should be monitored and, if possible, kept as low as possible. Monitoring of compressed air consumption is recommended in all cases.
In addition to compressed air consumption, quality is clearly a primary concern for many bulk materials. For example, the air used to convey powdered medicines or foodstuffs such as flour or sugar should be free of water, oil, or other particles.
As in any compressed air system, leakage can increase energy consumption exponentially. Regularly monitoring the tightness of the system can save big money.
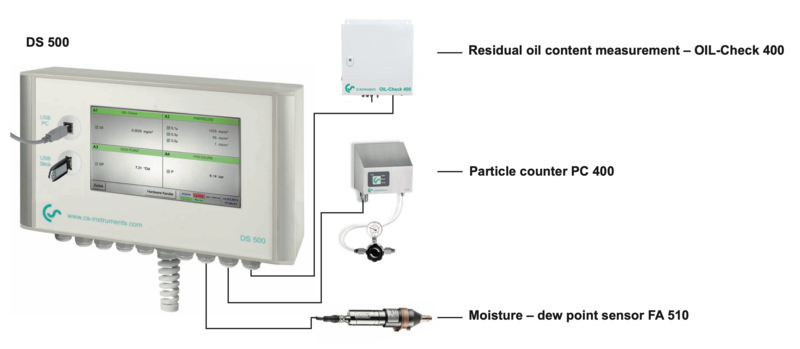
ISO 8573 consists of the following parts, under the general title Compressed air:
Usage for compressed air:
- Part 1: Contaminants and purity classes
- Part 2: Test methods for oil aerosol content
- Part 3: Test methods for measurement of humidity
- Part 4: Test methods for solid particle content
- Part 5: Test methods for oil vapour and organic solvent content
- Part 6: Test methods for gaseous contaminant content
- Part 7: Test method for viable microbiological contaminant content
- Part 8: Test methods for solid particle content by mass concentration
- Part 9: Test methods for liquid water content
ISO 8573-1:2010 Class | Oil | Water | Solid particles | ||
Total share of oil (liquid aerosol and fog) | Vapour pressure dew point | Maximum number of particles per m3 | |||
mg/ m3 | 0,1 – 0,5 μm | 0,5 – 1 μm | 1 – 5 μm | ||
0 | In accordance with specification by the device user, stricter requirements than class 1 | ||||
1 | 0,01 | <= -70 °C | <= 20.000 | <= 400 | <= 10 |
2 | 0,1 | <= -40 °C | <= 400.000 | <= 6.000 | <= 10 |
3 | 1 | <= -20 °C | – | <= 90.000 | <= 1.000 |
4 | 5 | <= +3 °C | – | – | <= 10.000 |
5 | – | <= +7 °C | – | – | <= 100.000 |
6 | – | <= +10 °C | – | – | – |
7 | – | – | – | – | – |
8 | – | – | – | – | – |
9 | – | – | – | – | – |
x | – | – | – | – | – |
Oil aerosol content
Looking at ISO 8573-2, there are different test methods authorized to measure oil aerosol content.
The following table is taken from the ISO 8573-2 standard document. The measurement methods correspond to a temporal sample. The results can therefore be used for validation.
Parameter | Method A – Full flow | Method B – Full flow | Method B2 – Partial flow |
Contamination range | 1 mg/m3 to 40 mg/m3 | 0,001 mg/m3 to 10 mg/m3 | 0,001 mg/m3 to 10 mg/m3 |
Max. velocity in filter | See 7.1.2.10 | 1 m/s | 1 m/s |
Sensitivity | 0,25 mg/m3 | 0,001 mg/m3 | 0,001 mg/m3 |
Accuracy | ± 10% of actual value | ± 10% of acutal value | ± 10% of actual value |
Max. Temperature | 100 C° | 40 C° | 40 C° |
Testing time (typical) | 50 h bis 200 h | 2 min bis 10 h | 2 min bis 10 h |
Filter construction | Coalescing line filter | Three-layer membrane | Three-layer membrane |
For online measurements, which will give the user a continuous readout, also an indication of peak contamination conditions, modern methods like PID sensor technologies are being used. These sensors offer a permanent, highly precise oil vapour measurement by ma- king use of the photo-ionic-detector method (PID).
The sensors can easily get connected to the compressed air system through a ball valve or quick coupler and analyse the air on a conti- nuous base. Long term stability can be insured by making use of a catalytic converter in order to burn off all hydrocarbons present in the air, hence making the air ideal to use for period zero calibrations while running.
The readouts are continuous and can be recorded as well as trigger alarms if limit values are breached. This corresponds to the main advantages compared to the temporary measurement method.
Residual oil content measurement – OIL-Check 400
The Oil-Check 400 enables permanent and highly precise measurement of the vaporous residual oil content from 0.001 mg/m3 to 2.5 mg/ m3. Due to the minimum measured value of 0.001 mg/m3, the compressed air quality class 1 (ISO 8573) can be monitored. This means that the entire measuring range can be monitored with the Oil Check.
Measurement of humidity
ISO 8573-3 looks at test methods for the measurement of humidity.
This next table has been taken out of the ISO 8573-3 standard document:
Method in order of uncertainty | Uncertainty ±°C | Range for humidity level expressed as pressure dew point° , °C | Remarks | ||||||||
Method | Table | -80 | -60 | -40 | -20 | 0 | +20 | +40 | +60 | ||
Spectroscopic | 2 | a | Detection limit for water va- pour is about 0,1 x 10-6 to 1 x 10-6 b | ||||||||
Condensation | 3 und 4 | 0,2 bis 1,0 | |||||||||
Chemical | 5 | 1,0 bis 2,0 | |||||||||
Electical | 6, 7 und 8 | 2,0 bis 5,,0 | |||||||||
Psychrometer | 9 | 2,0 bis 5,0 | |||||||||
a The uncertainty is not yet available in °C. |
The spectroscopic and condensation methods are very accurate but also very expensive to use as continuous measuring solutions. The chemical and psychrometers are spot checks which can’t be used for continuous measurements. The most commonly used method to measure humidity levels and dew point temperatures are the electrical method. The most commonly used sensors in this category are sensors based on capacitance.
This is due to the fact that these sensors offer the greatest measuring range with very good accuracies and repeatabilities.
These sensors can also easily be installed through a ball valve or a quick coupler and give continuous measurements which can be recorded and/ or used to trigger alarms if limit values are breached.
Moisture – dew point sensor FA 510
FA 510 measures the pressure dew point down to -80 °Ctd. Also in this case the continuous measurement takes care that alert is triggered immediately if the compressed air dryer breaks down. The sensor enables permanent monitoring of the compressed air dryer.
Particle content:
ISO 8573-4 looks at test methods for solid particle content.
This next table has been taken out of the ISO 8573-4 standard document:
Method | Applicable concentration range particles/m3 | Applicable solid particle diameter d μm | |||
< 0,1 | 0,5 | 1 | < 5 | ||
Laser particle counter | 0 – 105 | ||||
Condensation nucleus counter | 102 – 108 | ||||
Differential mobility analyser | – | ||||
Scanning mobility particle sizer | 102 – 108 | ||||
Sampling on membrane surface in conjunction with a microscope | 0 – 103 |
The most commonly used test method for measurement of solid particle content by counting is by using laser particle counters. The sensors can easily get connected to the compressed air system through a ball valve or quick coupler and analyse the air on a continuous base. Accuracy is influenced by the size of the laser diode and optics in use as well as the flow rate through the instrument. The greater the air volume that can be analysed at a particular time the higher the achieved accuracy.
Some laser particle counters only measure down to a particle size of 0.3μm (microns). This is not adequate for the food industry as particle sizes down to 0.1μm need to be detected in order to be able to determine the ISO 8573 classes.
Particle counter PC 400
The highly precise, optical particle counter PC 400 measures particles from a size of 0.1 μm and is therefore suitable for monitoring the compressed air quality class 1 (ISO 8573).
DS 500 - the intelligent chart recorder of the next generation
The centerpiece of comressed air quality measurement is the chart recorder DS 500. It measures and documents the measured data of the sensors for residual oil content, particles and moisture. The measured values are indicated on a 7” colour screen. The curve progres- sions from the beginning of the measurement can be viewed by an easy slide of the finger.
The integrated data logger stores the measured values safely and reliably. The threshold value can be freely entered for each measured parameter. 4 alarm relays are available for automatic alarm in case of threshold value exceedance.
Optionally DS 500 can be upgraded with up to 12 sensor inputs. For connection to a PLC DS 500 has an Ethernet interface as well as a RS 485 interface. The communication is done via the Modbus protocol.