Residual moisture measurement in fuel gases of the 2nd gas family
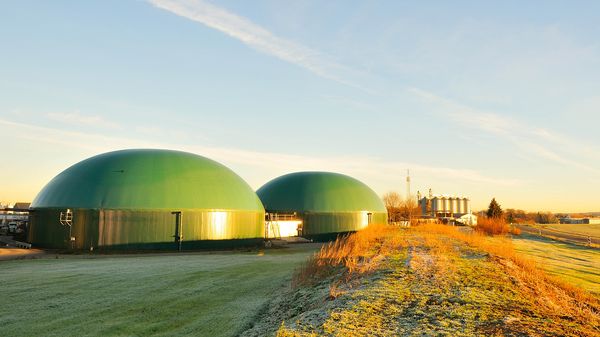
The 2nd gas family includes the fuel gases -natural gas and hydrogen as well as gases such as sewage gas or biogas.
According to the DVGW (Deutscher Verein des Gas- und Wasserfaches e.V. – German Technical and Scientific Association for Gas and Water), limits have been set for gas components that may be contained in fuel gases for feeding into the public gas network. To avoid possible subsequent technical problems as well as discrepancies in billing at the legal entity border, the feed into the gas network must be interrupted in the event of non-compliance with these specifications.
In addition to limits for impurities such as sulfur, ammonia, or silicon, etc., there are also specifications for water content, which plays an important role in the combustion performance of fuel gases and in avoiding technical problems.
Thus, the limit values for water content during feeding are defined as follows:
Designation | Unit | Limit |
Water content | mg/m3 | 200 (Maximum Pressure ≤ 10 Bar) |
50 (Maximum Pressure > 10 Bar) |
If these values are converted to the dew point temperature, i.e., the temperature below which water vapor precipitates as condensate, the following results are obtained:
Designation | Unit | Limit |
Dew Point Temperature | °Ctd
| -33° (Maximum Pressure ≤ 10 Bar) |
-46° (Maximum Pressure > 10 Bar) |
The residual moisture content is defined based on the coldest temperature ever measured; any pressure and temperature fluctuations must also be considered to exclude condensation.
For example, when feeding in any fuel gas, care must be taken to ensure that the water content is not exceeded. This can be measured and monitored with suitable measuring instruments.
Especially in winter, or in cold weather, critical components can be damaged by icing. In the worst case, this can lead to a shutdown of the gas supply, as no more gas can flow through the pipes due to repairs.
Apart from the technical problems, too much water leads to a reduction in the standard gas volume, because the more water there is in a standard cubic meter, the lower the burner efficiency, since more energy is needed to evaporate the water. Additional temperature fluctuations exacerbate the problem. For example, when delivered to the end customer, the standard volume is considered, which, measured at 1013.25 mbar and 0°C, is 1000 Nm3 at a water content of 0% RH (0°C). However, if this standard volume is converted to actual, real conditions, e.g. to 20°C and 970 mbar abs., with a water content of 60% r.h., only 880 m3 of fuel gas is obtained instead of the 1000 Nm3.
Since conventional flow meters for fuel gases are not pressure and temperature compensated and therefore do not measure the standard volume flow at 1013.25 mbar and 0°C, but only the volume flowing past under the current ambient conditions, if the water content is too high or the temperature fluctuates too much between the standard and actual volume flow measurement, you often deduct more than you would expect.